Tailored Process Proposal
Separation and enrichment technology of low-grade manganese ore
Concentrate, middling and tailings can be obtained by crushing and screening the ore, separating the non-valuable gangue in the ore, and then gravity separation or magnetic separation according to the characteristics of the ore; The middlings of gravity or magnetic separation are further processed, and then subjected to magnetic sweeping or chemical beneficiation for enrichment and recovery.
Hydrometallurgical technology of laterite nickel ore
The hydrometallurgical processes of laterite nickel oxide ore mainly include high-pressure acid leaching, mild acid leaching, and reduction roasting ammonia leaching combined with the fire method and wet method. According to the different content relationships of nickel, cobalt, magnesium, silicon, and aluminum in laterite nickel oxide ore, an appropriate process scheme is selected to maximize economic benefits.
GBT 6516-2010 Electrolytic Nickel Chemical Composition Standard
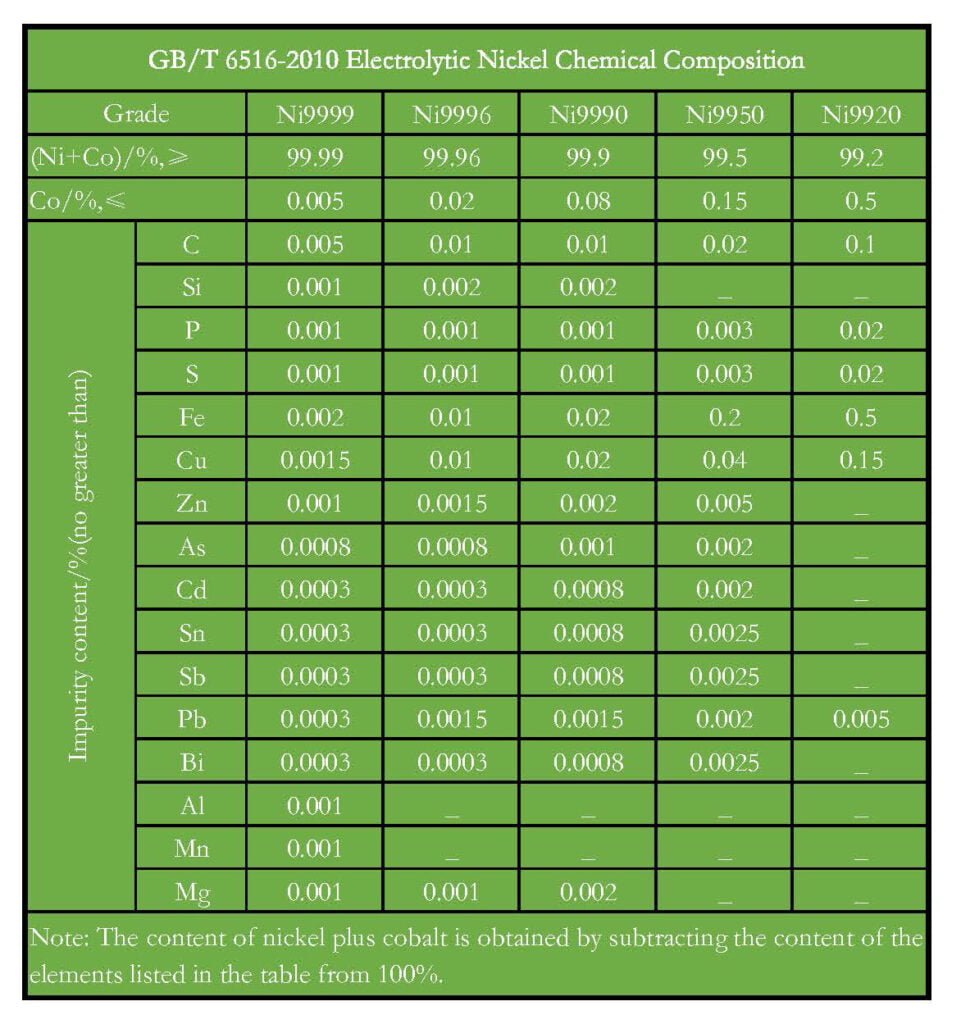
Pyrometallurgical technology of laterite nickel ore
Pyrometallurgy of laterite nickel ore mainly deals with metamorphic peridotite ore with high nickel content. Smelting processes mainly include rotary kiln drying rotary kiln reduction electric furnace smelting (rkef), sintering blast furnace reduction smelting, reduction magnetic separation electric furnace smelting and other methods. Its products are mainly ferronickel alloy and nickel matte products. Ferronickel alloy is mainly used to produce stainless steel. Nickel matte can be further blown to produce high nickel matte or directly used in hydrometallurgy.
Beneficiation technology of low-grade copper ore
The main types of copper deposits are porphyry copper deposits, layered copper deposits, copper-bearing pyrite, and skarn copper deposits.
For low-grade copper ores, targeted mineralogical research and exploratory tests are carried out to determine the beneficiation process. For copper sulfide as the main mineral of copper, flotation is the main beneficiation method.
YS/T 318-2007 Copper Concentrate Standard
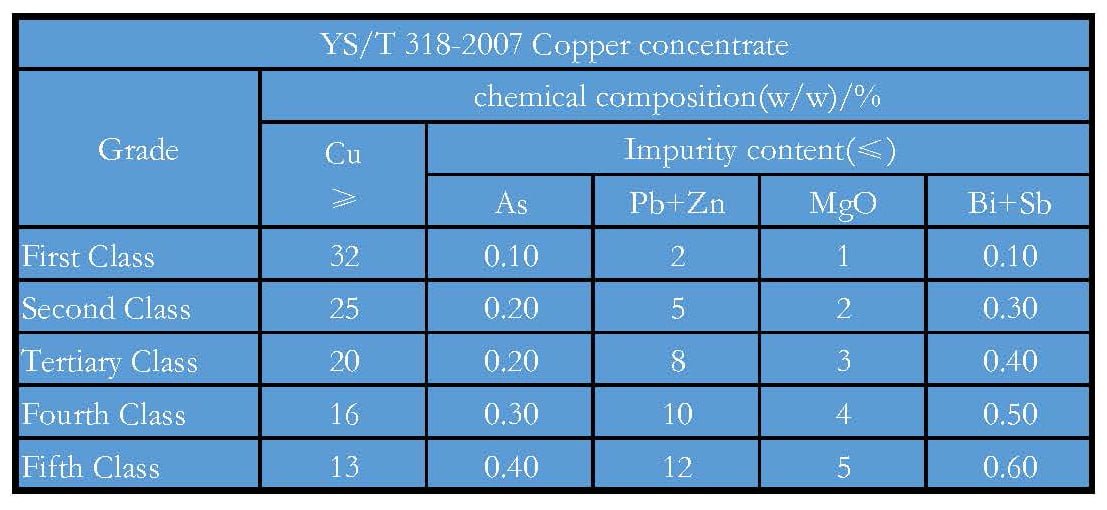
Hydrometallurgical technology of copper ore
With the continuous depletion of copper resources, the grade of copper ore is getting lower and lower, and the copper hydrometallurgy process has developed rapidly. At present, the main leaching methods of copper sulfide include oxygen pressure acid leaching, pulp electrolysis, and microbial leaching. According to the ore composition and mineral physical properties, select the appropriate process scheme.
Hydrometallurgical technology of zinc concentrate
Oxygen pressure acid leaching iron vanadium purification electrowinning process is a typical process for hydrometallurgical extraction of zinc from zinc sulfide concentrate. The advantage is that it can convert the sulfur in zinc sulfide concentrate into elemental sulfur, so the production of zinc does not need to be equipped with a huge flue gas treatment system and acid-making system, and the main process of zinc is no longer restricted by the sulfuric acid market.
GB/T 470-2008 Zinc ingot chemical composition
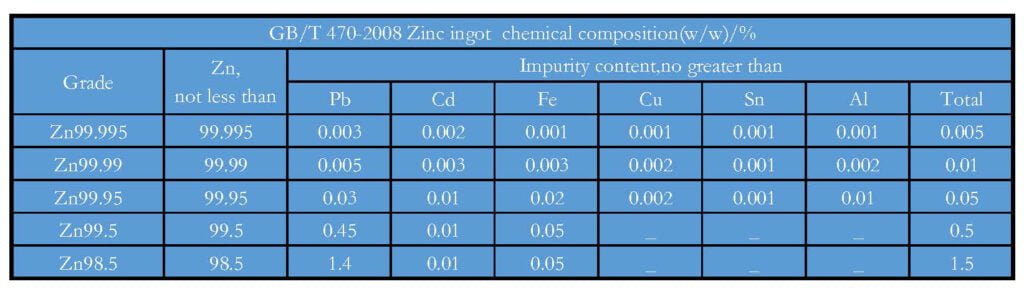
About Us
Jiangsu Metallurgy Engineering Technology Co., Ltd. specializes in nonferrous metal mineral mining, smelting engineering design, consulting, and construction management. We offer comprehensive services, including technical consultation, engineering design, equipment manufacturing, and general contracting for mining and metallurgy projects.
We collaborate with leading research institutes in China to develop innovative technologies and equipment. Committed to the “One Belt, One Road” initiative, we provide cost-effective solutions and reliable equipment. Our trusted services span the entire production process of beneficiation, hydrometallurgy, and pyrometallurgical production of nickel alloy.
Request a Quote
Ready to Work Together? Build a project with us!